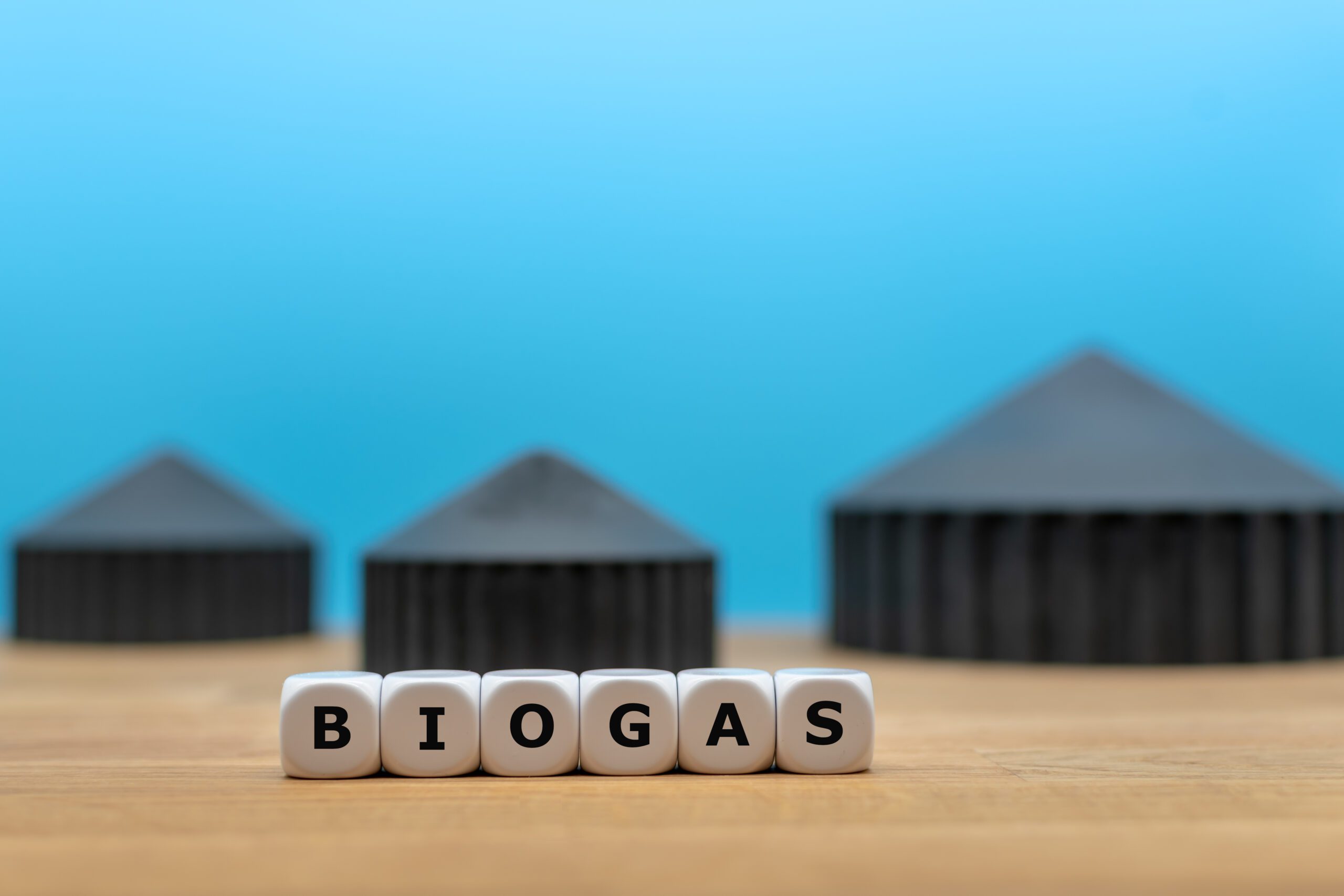
Every AD plant is different, even those built by the same technology providers. It is essential for operators to know how their plant runs and what its limits are.
Most problems within AD stem from trying to run a plant beyond its technical limitations. In this latest blog our Technical Sales Executive, David Lisle, recommends a list of items that as an operator, you should be familiar with;
Digester Mixing Capacity – Can you mix the tanks with the solids that are being added. Not just in optimum conditions but when things go wrong.
Pumping Capacity – Can you physically pump the material at a suitable rate, what is the dry matter limit before your pumps start to struggle.
Feeder Capacity – The maximum volume of feed that can be fed. Also, which feedstocks you can/can’t physically feed. A feedstock that is free might be your most expensive feed if it causes your feeding rates to drop by 25%.
Feed Types – Some plants simply aren’t designed to handle some feeds (e.g. maceration). Other feedstocks should simply be avoided (this is more of a personal preference).
Solids Removal – Make sure your site can remove solids/digestate at a suitable rate and you have storage for it.
Management/Finance teams listen – It is essential to listen to your operators if they’re regularly reporting faults.
Be proactive – Operators & Management must be proactive as it reduces the frequency you have to be reactive.
Physical checks – Always conduct the site checks and act up on any warning signs.
Proactive Maintenance & Dosing – Being proactive on maintenance and dosing is the biggest difference between most sites (up to 90% output) and exceptional sites (95+% output). Some examples are:
- Iron, trace element, enzyme, buffer dosing to maintain optimum conditions. Should you have any issues the effects aren’t as debilitating.
- Feeder/pump repairs to maintain feeding rates. Ensure you keep either a duty stand by or suitable spares so the main feeding equipment can be repaired within hours. Waiting 7-14 days for a part is just false economy.
- CHP/upgrader works & larger site maintenance (mixer replacements) planning to limit down time to a 5-10days.
Health and Safety – This is to protect you! No matter how inconvenient. AD plants are dangerous and there is generally a poor attitude to H&S and compliance in the industry. Operators need to be aware at all times of potential hazards (This is generally much easy with good housekeeping) and report anything they’re concerned about. If you don’t think its safe and it hasn’t been properly assessed don’t do it.
Compliance – Check paperwork and adhere to the permit. Compliance procedures are put in place to protect everyone, this includes the operator. The TCM should be ensuring that any material that enters or leaves site is compliant.